LABORATORY GRAPHITIZATION FURNACES
The laboratory graphitization furnace uses medium frequency induction heating, with a maximum temperature of 3200°C, which can meet all ultra-high temperature needs.
The diameter 100mm*high 200mm (orφ200*300mm, or larger) usable hot zone is suited for small batch processing or material research at ultra high temperatures.
LABORATORY GRAPHITIZATION FURNACES
The laboratory graphitization furnace adopts a compact integrated furnace design. The system is supported by a single frame platform which supports the furnace, vacuum system, and electronic cabinet containing the software controls. So it is small in size and requires only a minimum operating space. Install the casters under the frame, allowing the entire system to move easily. It is specially designed and produced for universities, scientific research institutes, and industrial research laboratories.
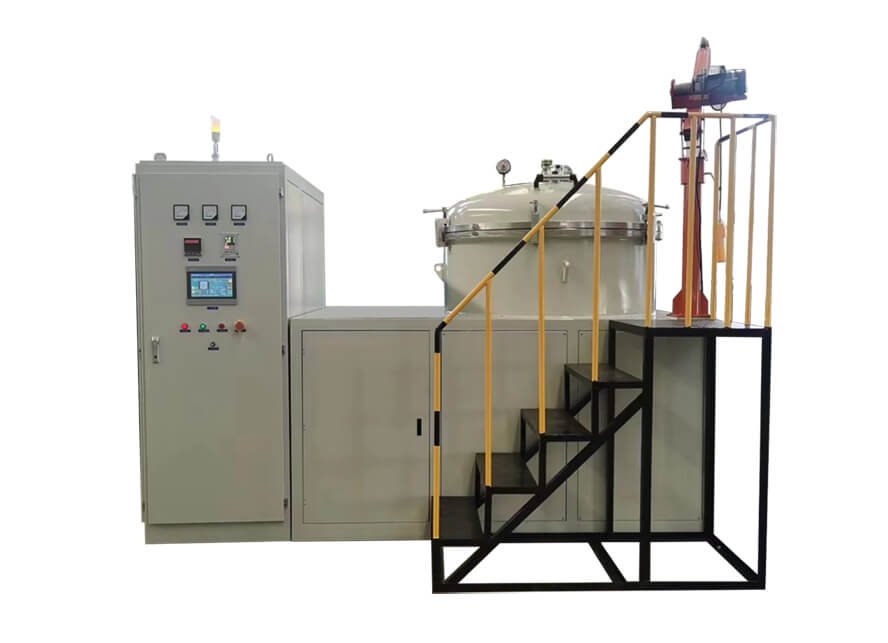
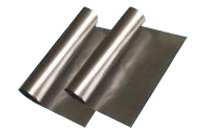
LABORATORY GRAPHITIZATION FURNACES APPLICATION
WHY WE CAN ACHIEVE ULTRA HIGH TEMPERATURE 3200 ℃ ?
Why we can achieve ultra high temperature 3200 ℃ for graphitization to the optimum grade for your application?
The laboratory graphitization furnace adopts medium-frequency induction heating method. A graphite susceptor is heated by induction. The energy is then transmitted to the treated parts by radiation.
Use graphite hot chamber that can withstand extremely high temperatures. High-purity and high-quality graphite susceptor is surrounded by the graphite insulation.
Pyrometer measures and controls temperature as under Argon environment, the maximum temperature is 3200 ℃. An sliding thermocouple can be added as an option to measure temperatures at the beginning of the process as the initial temperatures are not high enough to be detected by the pyrometer.
Special designed induction coils for rapid and efficient heating, and excellent thermal uniformity.
Flexible and highly efficient IGBT power supply
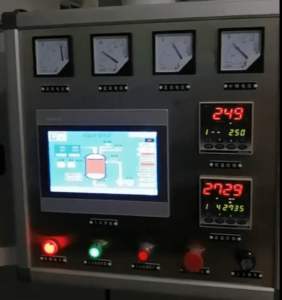
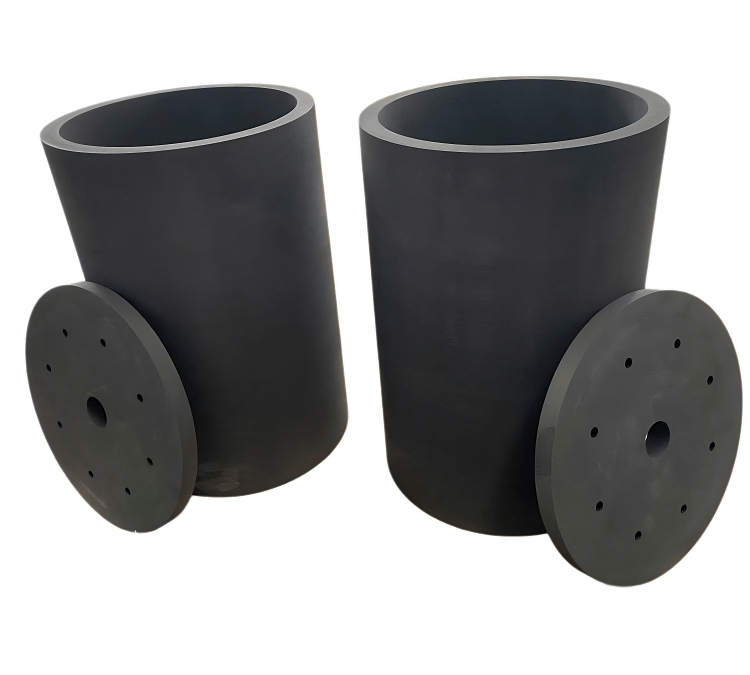
LABORATORY GRAPHITIZATION FURNACES FEATURES
graphitization furnace are equipped with advanced control systems to precisely set the desired temperature, monitor vacuum levels and more.
- Operation is available with manual or automated controls. For the manual version, all valves and pumps are operated by simple push buttons at the user panel. The automated software is operated via a touch panel interface. Data logging is possible for both manual and automated operation.
- Compact integrated design, small footprint, equipped with casters for easy movement and positioning.
- The top loading configuration provides excellent thermal uniformity and is a proven economical design. The access lid is pneumatically operated for easy access.
- The insulation layer is made of hard or soft composite graphite felt, which has a good insulation effect, small heat loss, and long service life.
- The vacuum system mainly speeds up the replacement of inert gases, and high vacuum is optional
- Use an optical pyrometer to measure and control temperature (1000℃-3200℃). Equip with a thermocouple (0-1600°C) for low-temperature, which can automatically switch between high and low temperatures to achieve full temperature control.
- The main components are imported from well-known brands, with high measurement and control accuracy.
Optional configuration:
- Chiller/Cooling Tower – for closed-loop cooling
- Gas purifiers – used to remove impurities from gas supplies
- High vacuum
- Diesel generator -provide the power to cooling water system when power failure
- CE certification- for export to international countries requiring CE
LABORATORY GRAPHITIZATION FURNACES CONTROL SYSTEM
Modern HTFs are equipped with advanced control systems to precisely set the desired temperature, monitor vacuum levels and more. Thermocouples measure and control temperature up to around 1500℃, while pyrometers are used above that temperature. User control is achieved through push-button panels, selector switches, and discrete controllers, or more advanced systems through an HMI computer interface.
A graphite susceptor is heated by induction. The energy is then transmitted to the treated parts by radiation. Use graphite hot chamber that can withstand extremely high temperatures. The susceptor is made of high-purity and high-quality graphite. And it is surrounded by the graphite insulation material.
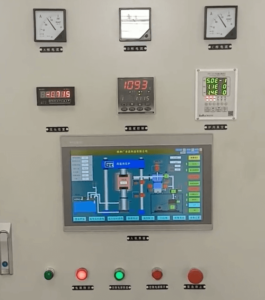
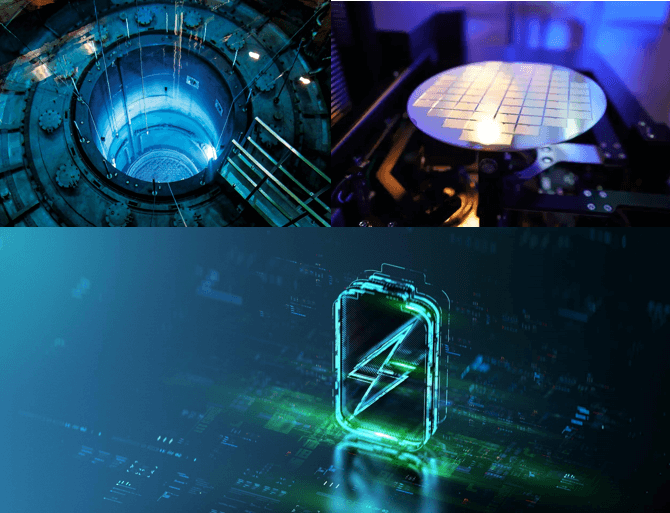
THE APPLICATION AREAS OF LABORATORY GRAPHICATION FURNACES
Clean Energy Applications
This kind of furnace has numerous applications in the clean energy sector. From research and development to manufacturing, HTFs have an important role to play in clean technology.
Semiconductor Manufacturing
HTFs are used in multiple stages of the semiconductor manufacture process. Their high temperature ranges are perfect for annealing silicon wafers, essential for the doping process. Solid-state synthesis, an efficient method for creating semiconductor materials, is also performed in HTFs.
Semiconductor materials are essential for clean energy, as they not only enable the processing ability that serves smart devices but are also used in renewable energy capture and storage. Further, high-performance light-emitting diodes (LEDs), which exploit semiconductor properties, can be manufactured effectively with HTFs.
A typical HTF incorporates the following components and designs to reach the desired temperatures.
The hot zone comprises the heating element and further insulation. Modern HTFs utilize fibrous graphite for its extremely high-temperature insulation properties.
Nuclear Energy
HTFs are used in the nuclear industry to create reliable, durable equipment for nuclear fuel and uranium enrichment used in cleaner power generation. HTFs can also be used to manufacture equipment for hot or cold cells meeting the strict standards necessary for nuclear energy generation.
maximum temperature
3200°C
Multiple stoves to choose from
From mini graphite furnace to large scale industrial type
Customizable production
Customizable production according to your needs
CONTACT US
We will reply to you within 24 hours and provide you with professional and high-quality services. At the same time, we will abide by the privacy protection agreement to ensure the security of your information.
- sunny@cnequips.com
- +86 18173379676
- Cemented Carbide Industrial Park, Tianyuan District, Zhuzhou City, Hunan Province