Author: Xiong Yan, associate professor of Hubei University of Technology
The SPS spark plasma sintering process pressure’s loading timing will affect the material’s performance.
Generally, except for the difference in heating mode, SPS has many similarities with traditional HP technology. Therefore, many scholars routinely compare SPS with traditional HP technology in their research on the densification mechanism of SPS. Some classic pressure-assisted sintering models have also been revised and borrowed in the study of SPS.
Bernard-Granger et al. studied the SPS sintering behavior of 3Y-TZP nanoceramics under a pressure of 100 MPa by introducing a “stress-rate” model. It pointes out that it dominates the sintering behavior by different densification mechanisms at different densities and effective pressure stages. A typical experimental phenomenon of the SPS process is the speedy densification rate when the density is roughly 50% to 90%. The maximum densification rate can reach the order of 10−3/s in solid-phase sintering and as high as 10−2/s in liquid-phase sintering.
Xu et al. studied the adequate activation energy in the early stage of the SPS process of 3Y−TZP nanoceramics with the help of four classical pressure-assisted sintering models based on atomic diffusion-related operations. The results show that the experimental value is much lower than the theoretical calculation value. Langer et al. compared the SPS and HP sintering behavior of the three materials and attributed the rapid densification of the material under SPS conditions to higher pressure.
High-temperature plastic deformation of the material is the primary mechanism for densification.
Due to the high modulus of elasticity of ceramic particle materials, plastic deformation of the particles is generally not the primary mechanism of densification in traditional HP techniques. As mentioned earlier, the SPS process uses higher pressures than conventional HP. Gendre et al. observed many dislocation defects at the grain boundary and within the grain during the SPS densification process of zirconium carbide materials. They proposed that the high-temperature plastic deformation of the material is the primary mechanism of densification. Ji et al. recently also reported that prepare B4C ceramics by SPS technology with plastic deformation as the primary densification mechanism.
The traditional HP process is generally a static external force load. Xie et al. recently proposed a new technology of oscillating pressure wave and thermal field coupling sintering—oscillating hot pressing sintering. And it has been successfully applied to preparing materials such as zirconia and silicon nitride. Compared with traditional HP technology, oscillating hot pressing sintering has apparent advantages in preparation efficiency and material properties.
The SPS equipment converts the AC power into DC pulses through a filter to heat the sample, and the pulse ratio of the equipment optimization setting is 12:2. Salamon et al. successfully introduced oscillating pressure in the SPS process by adjusting the device pulse ratio. In addition, it is also possible to set the pressure output in SPS to realize the texture of the material microstructure in the way of “Hot Forging.” Zhao et al. hot forged Bi2Te3 in SPS, which effectively improved the thermoelectric and mechanical properties of the material.
The step-by-step pressurization method in the SPS spark plasma sintering process improves material properties.
In the SPS process, fully apply the target pressure to the sample in the early sintering stage. When Wang et al. used SPS technology to prepare transparent MgAl2O4, they found that as the pre-pressure applied to the sintered powder increased at the low-temperature stage, the uniformity and optical transmittance of the final sintered body decreased. NIMS researchers also observed a similar experimental phenomenon in preparing transparent Al2O3 ceramics. And it is pointed out that the method of step-by-step pressure in the SPS process is beneficial to improve the light transmittance of fine Al2O3 ceramics under a high heating rate. Santanach et al. believe that the step-by-step application of pressure is more conducive to promoting the slip and rotation of the powder at high temperatures.
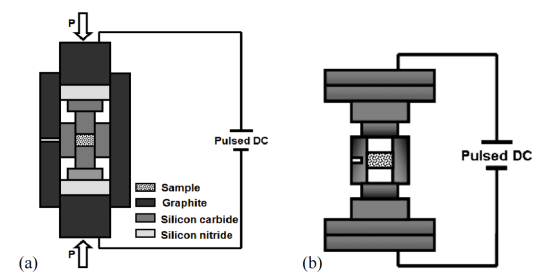
Schemes of the dies used for (a) high-pressure and (b) pressureless spark plasma sintering