Author: Xiong Yan, associate professor of Hubei University of Technology
SPS Spark Plasma Sintering equipment can realize the adjustment of heating rate in a relatively wide range.
SPS Spark Plasma Sintering Equipment provides a convenient heating rate control method. It can realize the adjustment of heating rate in a relatively wide range. High-speed heating can effectively inhibit the growth and maturation of grains during heating. So it often uses a faster heating system to prepare nano-ceramic materials. In addition, high-speed heating can make the sintering process far from the equilibrium state. It benefits the practice of heterogeneous structural materials and enriches the kinetics and thermodynamics of the sintering process. A typical example is that Shen et al. applied the “Dynamic Ripening Mechanism” in the SPS liquid phase sintering of Si3N4 ceramics. Under high-speed SPS temperature rise, the Si3N4 grains undergo anisotropic Oswald ripening to form Si3N4 long Columnar interlocking structure.
Some scholars have studied the relationship between heating rate and microstructure and the relationship between heating rate and densification under SPS conditions. They found that the larger the current and the higher the heating rate. The faster the densification rate of the sample, and the higher the final density. Therefore, some scholars believe that it increases the sintering rate as much as possible to obtain high-density sintered products. However, the National Institution of Materials Science (NIMS) in Japan found in the research on preparing transparent Al2O3 and MgAl2O4 ceramics by SPS that a lower heating rate is conducive to obtaining a sintered body with uniform color and good optical properties. It attributed the reason to the fact that low-speed heating is conducive to the diffusion of grain boundaries and the reduction of defect concentration.
“Two-Step Sintering” (TSS) technology in SPS Spark Plasma Sintering Equipment
Chen et al. proposed the famous “two-step sintering” (TSS) technology in 2000 to suppress the rapid growth of grains in the later stage of sintering. First, realize the “frozen microstructure” in the sintered body at a higher temperature. Then control the difference in grain boundary migration and grain boundary diffusion kinetics at a lower temperature to achieve densification of the material while inhibiting the growth of grains.
Schwarz et al. applied this technology to the SPS process of cubic phase YSZ materials. They found that it can effectively inhibit grain growth and improve materials’ preparation efficiency. The concept of “two-step sintering” was first proposed in 1997 by researchers at the University of California, Berkeley. In preparing alumina materials, they first homogenized the microstructure by keeping it warm for a long time at low temperatures, then densified it at high temperatures. The two-step process inhibits grain growth. This concept was successfully borrowed into the SPS process by Chen et al. Recently, Reddy et al. proposed a multi-stage distributed sintering process of the SPS process and applied it to the preparation of Al2O3 and 3Y-TZP nano-ceramics.
SPS Spark Plasma Sintering equipment adjusts the heating and cooling rate by adjusting the output current and voltage.
The fluctuation of current and voltage during the sintering process is more sensitive than the temperature. It provides an essential basis for more precise control of the sintering system. Taking the synthesis of TiB2 from Ti powder and B powder in SPS as an example, there is an instantaneous “overheating” in the temperature curve because the reaction is a strong exothermic reaction. A significant reduction in current and voltage output accompanies this.
Similar exothermic or endothermic reactions exist during the sintering of many materials. It is only in some cases that the heat is too small to affect the recorded curve and is ignored during the sintering process. However, in the sintering process of some nanomaterials, this instantaneous “overheating” phenomenon may become a severe hidden danger. This is because the sintering activity of the nanopowder is very high. It is easy to form agglomerates, and a little heat is enough to cause abnormal growth of the agglomerates. Local overheating can be prevented at this time by reducing the heating rate and prolonging the cooling time.
When Shen et al. prepared transparent nano-MgO ceramics, they considered that the initial nano-powder easily absorbed water and formed Mg(OH)2. And it will exothermically reduce Mg(OH)2 will to MgO at about 450ºC during heating. Therefore, it adopts a slow heating or heat preservation method near this temperature to prevent the abnormal growth of grains.
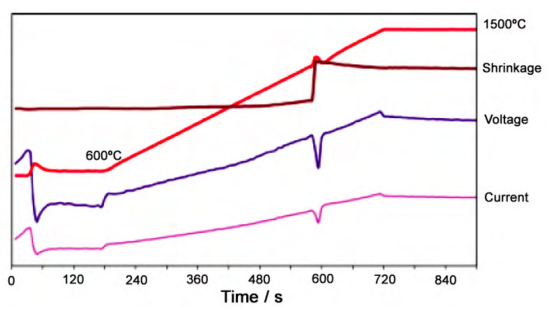
Adjusted through the current control mode (SPS-CCM)
Usually, the heating system of SPS is controlled by setting the heating rate, and the current value gradually increases as the temperature rises. In addition, the heating system of SPS Spark Plasma Sintering Equipment can also be adjusted through the current control mode (SPS-CCM). The temperature is raised with a certain constant current. The Sakka team used the CCM finite element method to model the SPS process’s temperature. And temperature field distribution and applied it to preparing ultrafine-grained WC materials. Niu et al. recently achieved ultrafast densification of pure B4C ceramics using a current-controlled heating mode.