We can experiment with our company (Chinaequips Industry Equipment Co., Ltd) SPS spark plasma sintering furnace. The furnace is also called FAST Field assisted sintering technique or DCS Direct Current Sintering press furnace system.
Experiment summary:
We prepare the W-Re high specific gravity alloy by SPS spark plasma sintering furnace. The sintering temperature was 1800℃, the sintering pressure was 40MPa, and the holding time was 5min. We conduct the density, hardness, and other performance tests on the W-Re alloy samples sintered by the FAST Field assisted sintering technique. It observed the samples’ metallographic structure and grain size with a metallographic microscope. The results show that we can achieve the densification of W-Re alloy at a lower temperature by DCS Direct Current Sintering press furnace system. And it can effectively control the grain growth to improve the hardness of the material.
1. Experimental steps:
1.1 Raw material preparation
In the experiment, we used W powder (purity ≥ 99.5%) and Re powder (purity ≥ 99.0%). And we mixed the powders according to a specific ratio, as shown in Table 1. Put the weighed alloy powder into a stainless steel ball milling tank; the grinding balls are stainless steel balls. Mill the powder with a low-energy ball for 24 hours at a ball-to-material ratio of 10:1. And a nominal speed of 500r/min. The average grain size of the W powder used in the experiment is about 10 μm. And the average grain size of the Re powder is about 20 μm.
Table 1 Composition ratio w/% of experimental samples
Samples | 1 | 2 | 3 |
Re w/% | 10 | 30 | 50 |
1.2 SPS spark plasma sintering process by Chinaequips SPS furnace
Weigh and place the prefabricated W-Re alloy powder in a Ø20mm graphite mold. Then we can sinter in the CNEQPS-SPS-2T2KA spark plasma sintering system manufactured by Chinaequips Industry Equipment Co., Ltd., to achieve densification. The samples were spark plasma sintered under vacuum conditions at a temperature of 1800 °C:
- The heating rate was 200 °C/min.
- The holding time was 5 min.
- The maximum pressure during sintering was 40 MPa.
1.3 Performance test
It determines the sample density by the Archimedes drainage method and weighs the piece’s mass with a BS210S electronic balance. It observes the samples’ metallographic structure and grain size under a LEICA DM4000M metallographic microscope. The Shimadzu HMV-FA2 Vickers hardness tester measured the hardness of the piece, and it took the arithmetic mean value of 3 points.
2. Results and Analysis after SPS spark plasma sintering funace
2.1 Relative density after sintering
Figure 1 shows the relative density map of the sintered W-Re alloy. We can see from the figure that under the sintering temperature of 1800 °C, the sintering pressure of 40 MPa. With and holding time of 5 min, the relative density of W-Re alloy increases first and then decreases with the increase of Re content.
When the Re content reaches 30%, the relative density of the alloy reaches 94.09%. The density of W-Re alloy can get more than 93.64% under experimental conditions. However, the diffusion of W and Re atoms in the matrix is insufficient due to the short holding time. So the sintering temperature of 1 800 ℃ did not obtain a fully dense high-density W alloy, only by prolonging the sintering holding time, increasing the sintering temperature to a specific range. Or, using a high-strength mold to improve the external pressure of the experiment, can a sufficiently dense high-specific-gravity W-Re alloy be expected to be obtained?
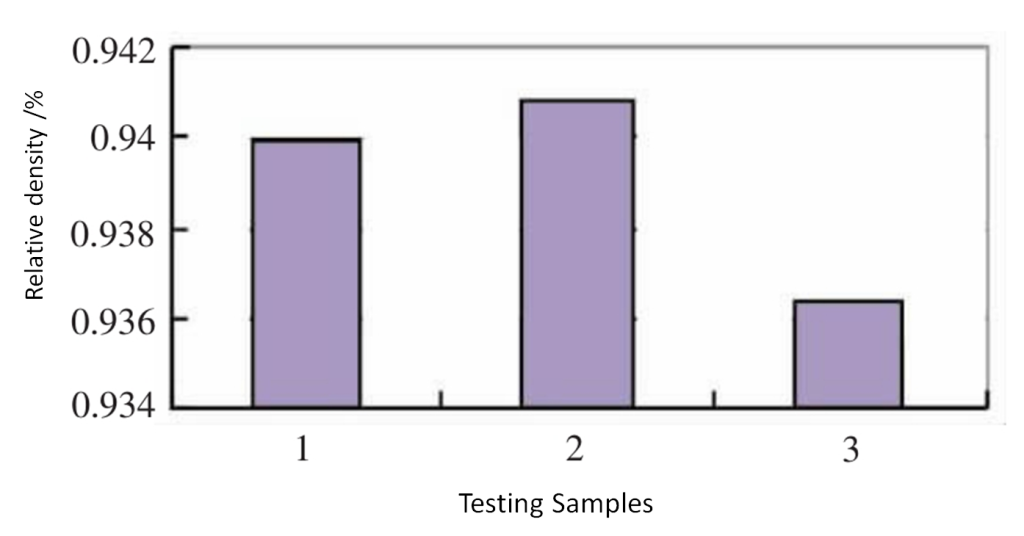
2.2 Relative hardness after sintering
We use the HMV-FA2 Vickers hardness tester to measure the hardness of the sample. Under the conditions of a load of 1.961N and a holding time of 10s, it shows the measured Vickers hardness of the W-Re alloy in Figure 2.
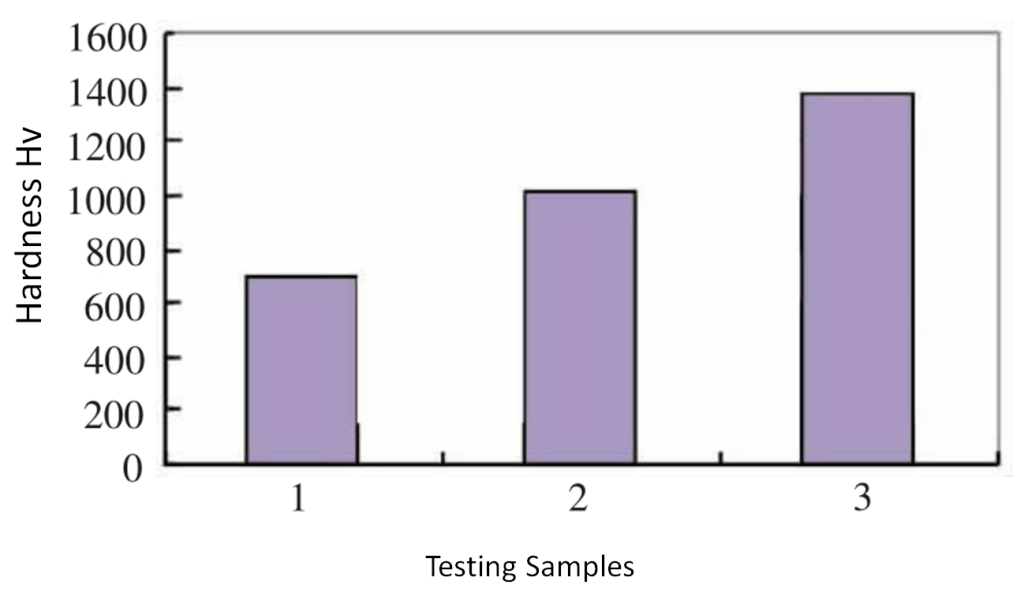
We can see from Figure 2 that the Vickers hardness of the W-Re alloy sample increases with the increase of the Re content in the alloy. From the W-Re binary phase diagram, it knows that W and Re, which are both body-centered cubic crystal structures. It can form an infinite solid solution, and Re atoms replace W atoms located on the lattice nodes in the W crystal, resulting in lattice distortion. Thereby increasing the position The resistance to wrong movement plays a role of solid solution strengthening. With the increase of Re content, during the SPS sintering process, more Re atoms can enter the W matrix to replace W atoms, resulting in more lattice distortion, thereby achieving a more significant strengthening effect and increasing the hardness of the alloy.
2.3 Metallographic analysis of samples after sintering
Figures 3 to 5 are the metallographic and microstructure photos of samples with different ratios of tungsten and rhenium after SPS sintering. It can see from Figure 3 that Re particles are evenly distributed on the tungsten substrate. W and Re particles are fine and maintain the original powder grain size, uniform distribution, abnormal grain growth, and no apparent agglomeration and segregation. However, it can still abserve the small pores due to the short holding time and low sintering temperature. In Figure 3 and Figure 4, it disperses the black Re particles in the W matrix, which differs from Figure 5. The latter has formed a polycrystalline structure through sintering. It results in a solid solution instead of a simple powder particle composite.
W-10% Re metallograph (*200)
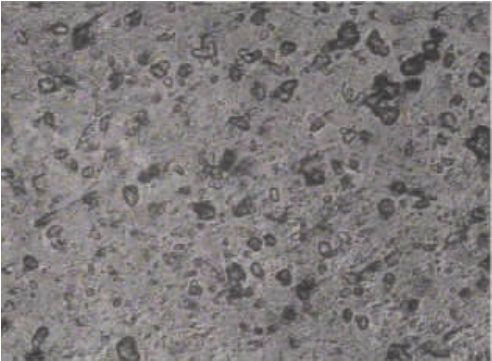
W-30% Re metallograph (*200)
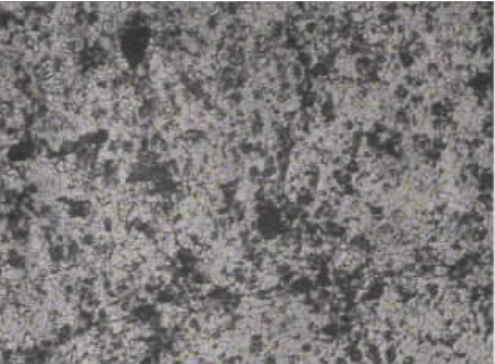
W-50% Re metallograph (*200)
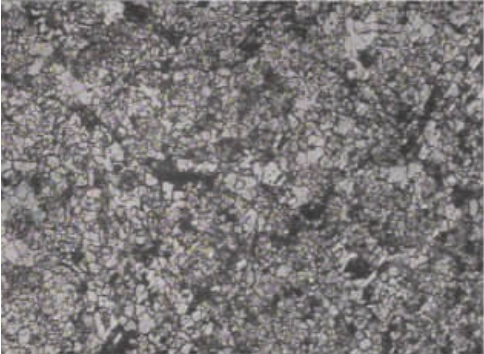
3. Conclusion
(1) Using spark plasma sintering technology can realize low-temperature solid-phase sintering of W-Re high specific gravity alloys.
(2) Under the process conditions of temperature 1 800 ℃, holding time 5 min, pressure 40 MPa, and vacuum degree about 1 Pa, the SPS sintered W-Re alloy has uniform microstructure, fine grains, and a relative density greater than 93.64%.
(3) The hardness of SPS sintered W-Re alloy can reach Hv700~1 300, and the hardness is higher. In addition to the solid solution strengthening effect of Re atoms, the grain structure of SPS spark plasma sintering furnace prepared materials is fine, and fine grain strengthening is also an important factor.