Author: Xiong Yan, associate professor of Hubei University of Technology
Compared with the traditional sintering method, it significantly improves the efficiency of material preparation and the performance of the prepared material. This technical feature makes SPS spark plasma sintering technology develop rapidly in the field of ceramic materials. Studies have shown that exceptionally high melting point materials with low diffusion coefficients, such as nitrides, borides, and carbides, can rapidly prepare at relatively low temperatures under SPS conditions.
The unique material preparation mode of spark plasma sintering improves the properties of sintered materials.
Spark plasma sintering SPS uses pulsed current to pass through the mold and conductive samples. It has higher thermal efficiency and can realize rapid heating and cooling of samples. Therefore, it can effectively inhibit the growth of grains during the heating process, retain the required high-temperature structure and phase composition, and realize the flexible regulation of the material’s microstructure. Similar to the traditional HP sintering, the SPS spark plasma sintering process can also apply external axial pressure to assist the sintering process. In the meantime, the pressure value is higher. Currently, the sintering pressure of the graphite mold can reach 100 MPa-150 MPa). And the material can be sintered at a lower temperature. Rapid densification, thereby reducing possible component volatilization and inhibiting the occurrence of undesirable phase transitions.
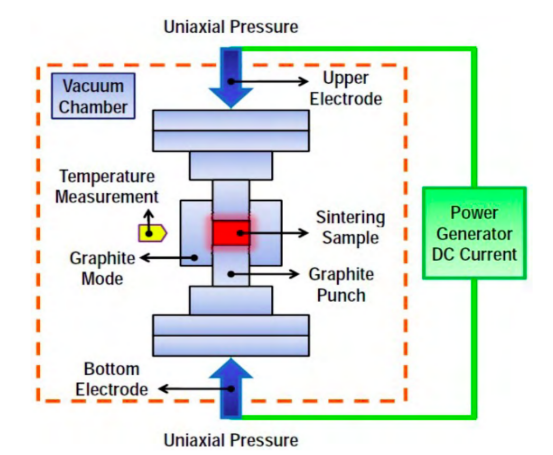
Schematic diagram of spark plasma sintering equipment
The following will discuss the existence and function of discharge/plasma in applying SPS technology in ceramic materials.
Prepare the bulk ceramic materials by sintering the ceramic powder, and one of the methods of activating sintering is to use an electric current. Because SPS technology uses low voltage and high pulse current heating methods, we also call it “Pulsed Electric Current Sintering.” Or “Pulsed Electric Current Sintering, PECS” or “Electric Pulse Assisted Consolidation” technology. As early as 1933, there was a report in the US patent on using pulse current or discharge to promote the sintering of metal powder. Then from the 1950s to the 1970s, American and Japanese scholars researched the “discharge sintering” technology.
One of the explanations for the rapid densification mechanism of SPS technology is the role of discharge and plasma excitation in the sintering process.
When using SPS technology to sinter metal powder, it is proposed that electric field-induced positive and negative electrodes are in the powder particle micro-area. Omori observed the “discharge neck” formed during the sintering process and the network “bridging” between powder particles. Under the action of electric current, it generates a discharge between the particles. Plasma is excited, and the plasma’s purification effect on the particles’ surface promotes sintering.
Ishiyam et al. believe it may generate the plasma between metal particles under pulse current. It plays a role in the sintering process and the formation of oriented grains. At the same time, it reduces the diffusion-free energy of metal atoms under the action of an electric pulse field. It accelerates atomic diffusion, and its resistance heating is also conducive to plastic deformation. So we also call SPS plasma-assisted sintering (Plasma-Assisted Sintering, PAS).
The explanation for the rapid densification of SPS in metallic materials is also “borrowed” from the sintering of non-conductive ceramic materials.
Some scholars attribute the rapid densification mechanism of SPS spark plasma sintering technology to the discharge between particles and plasma excitation during the sintering process. Through the simulation analysis of the SPS temperature field, Wang et al. believed that the region most likely to generate plasma during sintering is the region with the strongest electromagnetic field in the cavity (the area near the edge of the indenter). The region most likely to generate plasma during sintering time is the moment the current changes the most. However, most ceramic powders are not electrical conductors. The research by Tomino et al. shows that when the sintering current is 1000 A, the current passing through the non-conductive Al2O3 sample is less than 100 mA. The research by Carney et al. also shows that the change of the pulse current has no significant contribution in the current passing through the non-conductive sample.
Hulbert et al. used in-situ atomic emission microscope measurement, in-situ optical microscope observation, and ultra-fast in-situ voltage measurement to measure whether there is discharge plasma in the process of SPS sintering non-conductive ceramic materials, and haven’t found SPS spark plasma sintering process. There is a discharge phenomenon between particles or the existence of plasma. There needs to be more robust experimental evidence for the discharge and plasma in the SPS process of non-conductive materials.
It is generally believed that discharge/plasma is not a significant contributor to material densification or performance enhancement in non-conductive ceramic materials.