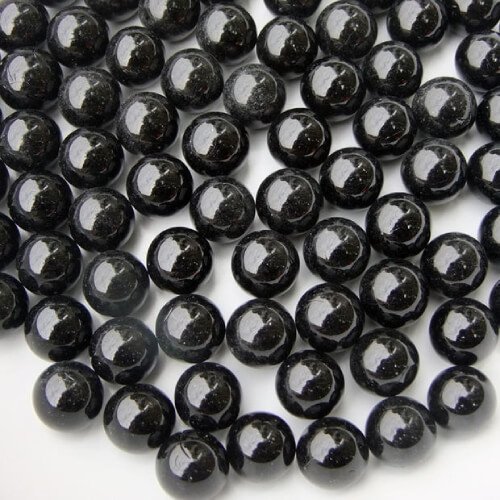
Due to its excellent mechanical, thermal, and electrical properties, zirconia has a wide range of applications in structural materials, optical components, oxygen sensing components, and fuel cells. In recent years, with the rapid development of people’s demand for decorations, black zirconia ceramics have become a new favorite material for high-end decoration due to their excellent mechanical properties, bright colors, metallic luster, and non allergic effects. They have broad market prospects in high-end watch chains, bracelets, mobile phone shells, and other products.
At present, the preparation of black zirconia ceramics mainly adopts the following two methods:
1. Blackening of zirconia ceramics in vacuum, reducing atmosphere, or inert atmosphere results in the formation of oxygen vacancies, leading to the formation of point defects in color centers and the absorption effect of light.
2. Doping iron, cobalt, nickel and other color oxides into zirconia enhances its light absorption by adding color pigments, thereby improving the hiding power and blackness of the zirconia material. When using a Vacuum furnace, a reducing atmosphere furnace or an inert atmosphere furnace, zirconia needs to be sintered into porcelain in the air, and then blackened in the above-mentioned sintering furnace, which greatly increases the cost of the production process. For products with special shapes and different thicknesses, it is easy to cause a series of problems such as color difference due to uneven color centers during the blackening process, resulting in insufficient blackness of the products. Doping iron, cobalt, nickel and other color oxides in zirconia can easily cause black to not black due to the inconsistent absorption wavelength of each oxide, resulting in product colors that are reddish, bluish, and greenish; Moreover, the added oxides are prone to react with yttrium and zirconium, disrupting the stability of zirconia and causing product phase transformation cracking, reducing the strength and hardness of the product. Therefore, the strength and hardness of existing zirconia ceramics are generally low; Moreover, due to the difficulty in controlling the doping amount of yttrium oxide and the high sintering temperature, it is easy to cause the coexistence of tetragonal and monoclinic phases in zirconia ceramics, which also poses great challenges in improving the strength and hardness of zirconia ceramics.