Author: Xiong Yan, associate professor of Hubei University of Technology
High Pressure Spark Plasma Sintering SPS technology (HP-SPS)
In order to prepare dense nanocrystalline ceramics, it is necessary to reduce the sintering temperature as much as possible to suppress the growth of grains at high temperatures. In 2006, the Munir team took the lead in developing the High Pressure Spark Plasma Sintering SPS technology (HP-SPS). And successfully prepared zirconia and ceria ceramics with a relative density greater than 98% and an average grain size of about 10 nm.
Figure 1 (a) shows a schematic diagram of the mold used in HP-SPS. It can increase the axial pressure of the SPS process to 1 GPa by means of mold nesting. Munir et al. believe that high pressure is conducive to rearranging particles and breaking agglomerates in the early sintering stage. The plastic or superplastic deformation of particles under high pressure at the later sintering stage is the key to promoting densification.
Warm Press Sintering Technology (WPS)
Since it uses a silicon carbide (SiC) indenter on the contact surface with the sample during the sintering process. It basically blocks the contact between the current and the sintered body. The heating of the sample is mainly through the heat conduction of the graphite jacket. Therefore, this method is more similar to traditional hot press sintering. Trunec et al. named this Warm Press Sintering Technology (WPS) sintering method. It greatly reduces the sintering temperature of the sample under high pressure. It effectively inhibits the ripening and growth of grains, and opens up a new method for preparing nano-ceramics.
Pressureless Spark Plasma Sintering SPS technology (PL-SPS)
Regarding the Pressureless Spark Plasma Sintering SPS technology (PL-SPS), the earliest literature report was a research work on synthesizing nanometer HfB2 powder in 2012. It shows the mold used in the PL-SPS technique in Figure 1 (b). Transforming the traditional graphite mold into a crucible shape completely blocks the application of external force and possible plasma/electric field and other factors. Make full use of the characteristics of high-speed temperature rise of SPS to suppress grain growth during nano-powder synthesis. Xie et al. first synthesized nano-ZrC powder using PL-SPS technology. And we have successfully realized the low-temperature preparation of fine-grained ZrC dense ceramics.
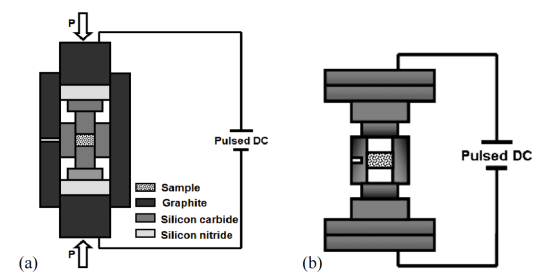
Fig. 1 Schemes of the dies used for (a) high-pressure and (b) pressureless spark plasma sintering
Design and Application of Mold in Spark Plasma Sintering Technology
Through the design of the mold, it is also possible to control the temperature gradient during the SPS sintering process. It provides convenience for the preparation of composite materials with large differences in sintering behavior, especially some functionally graded materials. Hong et al. used an asymmetric tapered mold to realize the preparation of ZrB2/SiC/ZrO2 laminated composites. Liu et al. realized the preparation of Ti2AlN/TiN FGMs from a single Ti/AlN raw material component by SPS temperature field regulation.
The mold used in SPS under laboratory conditions is generally a graphite mold with a single cavity and a symmetrical cylindrical structure. With the development of SPS technology and the requirements of large-scale industrial manufacturing, multi-cavity molds and some special shape molds have also been developed one after another. For example, NJS, a Japanese company, has realized the industrial production of large-size WC/Co−diamond cutting blades by lamination sintering.
The Al2O3 ceramic sandblasting nozzle prepared by SPS has higher hardness, surface finish and longer service life. It uses the spherical molds in the production of optical lenses (Fig.2). In addition, some new mold materials are also applied in the SPS process. At present, most SPS molds are made of graphite, with a resistivity of about 15 μΩm and a compressive strength of 100 MPa to 150 MPa. The graphite indenter with added carbon fiber can withstand a pressure of 400 MPa. For the sintering process at a lower temperature (not exceeding 1000ºC), molds made of WC-Co, Mo alloy, transparent quartz and even alumina ceramics have also been tried in the author’s research.

Fig.2 (a) WC/Co diamond cutting blade and (b) Al2O3 blasting nozzle by SPS. (c) Aspheric molds used in
SPS.