The vacuum sintering of cemented carbide began in the 1930s and achieved great development in the 1960s. Modern cemented carbide production mostly uses the vacuum atmosphere in the sintering furnace. The vacuum degree of cemented carbide vacuum sintering mostly belongs to the low vacuum range. Generally, it is 13.3-1.33 Pa. In fact, “low pressure” is more accurate than “vacuum”.
Compared with the hydrogen atmosphere, the vacuum atmosphere in the sintering furnace has the following advantages:
Improve the purity of the furnace atmosphere.
Reduce the influence of harmful impurities such as H2O, O2, and N2 on the quality of the alloy. Therefore, it avoids the decarburization reaction of WC due to water vapor, the oxygenation reaction of TiC, and the nitrogenation reaction of TiC and TaC.
During sintering, the free energy becomes negative due to the effect of vacuum, that is, pressure reduction.
It destroys the balance of MeO+C=Me+CO reaction. Developing the reaction to a new equilibrium is beneficial to reducing metal oxides and removing oxygen. The vacuum is beneficial to the desorption and removal of the gas adsorbed on the surface of the sintered body and the dissolved gas in the sintered body.
Since the surface of the solid is purified by vacuum, the capillary resistance in the sintered body is reduced.
Improves the wettability of the liquid phase to the solid phase. Especially tungsten carbide-based cemented carbide and carbide-based tungsten carbide-containing carbide pots.
The oxides of trace impurities, such as Si, Ag, Mg, Ca, S, etc., are easy to decompose or be reduced and removed under the vacuum.
The vacuum atmosphere in the sintering furnace is relatively simple and easy to control.
Increase the total carbon of the raw material WC.
It needs to pay attention to the oxygen adsorbed in the material, the oxygen dissolved in Co and WC (in ppm), and the oxygen in the form of a surface film. That is residual oxygen in all materials. In the heating stage, it reacts with the carbon (free carbon and combined carbon) in WC to generate CO. And pump the CO away. The oxygen content of WC-Co alloy is about from 0.5% peak to 0.06%, which reduces the carbon content of the alloy. Vacuum sintering of WC-Co alloys requires very strict carbon content control, generally in the mean of ±0.04%. Small fluctuations in carbon content will lead to obvious deterioration of the alloy structure, resulting in η or graphite phases. Therefore, it is necessary to increase the carbon content of the mixture, and it is best to increase the total carbon of the raw material WC.
Strictly control and reduce the oxygen content during the process of mixture preparation.
The loss of vacuum-sintered carbon is always proportional to the amount of “total” oxygen in the sintered body. If we know the “total” oxygen, we can predict the amount of carbon lost. And basically, the ratio of oxygen to carbon atoms is 1.33. The oxygen in the sintered body in actual production is variable and unknown. Therefore, try to control the oxygen content within the range we require. Only in this way, we can control the carbon content of the alloy within the required range. Because the oxygen content in the sintered body often fluctuates greatly, the process control of WC-Co alloy vacuum sintering is relatively difficult. Therefore, in a series of processes of mixture preparation, the oxygen content should be strictly controlled and reduced.
The type of forming agent is different, the process of removing forming agent and sintering is different, and the carbon content of raw material WC is also different.
Buna-Na rubber and hydrogen sintering is used, and WC with carbon content lower than the theory is selected. Choose WC with a slightly higher carbon content for paraffin and hydrogen sintering. Paraffin, hydrogen dewaxing, vacuum sintering, choose WC with a carbon content of 6.18~6.25%. The carbon content is even higher for Paraffin, vacuum dewaxing, and vacuum sintering.
The degree of vacuum affects not only the exhaust process but also the vacuum atmosphere in the sintering furnace and the evaporation loss of the bonded metal.
Depending on the pressure in the furnace, the nature of the furnace atmosphere will also change:
Increasing the degree of vacuum will facilitate the deoxidation reaction. Therefore, before the liquid phase appears, a higher degree of vacuum is used to make the deoxidation process more complete. After the liquid phase appears, the vacuum must be properly reduced. During vacuum sintering, the bonding metal cobalt has a higher vapor pressure. Cobalt evaporation loss depends on sintering temperature, sintering holding time, and vacuum degree. After the first two are determined for the process, it depends on the degree of vacuum. According to the data, at 1250°C, the vapor pressure of cobalt is P=0.02Pa. That is, cobalt will not volatilize basically under the condition of solid phase sintering. At 1400°C, P=0.37Pa. Therefore, the vacuum degree is controlled at 13.3~1.33 Pa at the end of the sintering stage. The evaporation loss of cobalt is significantly reduced.
In the 1970s, to prevent the loss of carbon, Pachar and Horvath used a hydrogen-methane atmosphere under reduced pressure or a small amount of methane to carburize the sintered body before sintering.
Currently, Chinaequips vacuum sintering furnace adopts an automatic program to control the gas hydrogen in the furnace. Various gases can be fed into the furnace, and the flow rate can be controlled. Chinaequips vacuum sintering furnace is also equipped with a furnace gas analysis device to ensure the atmosphere’s stability.
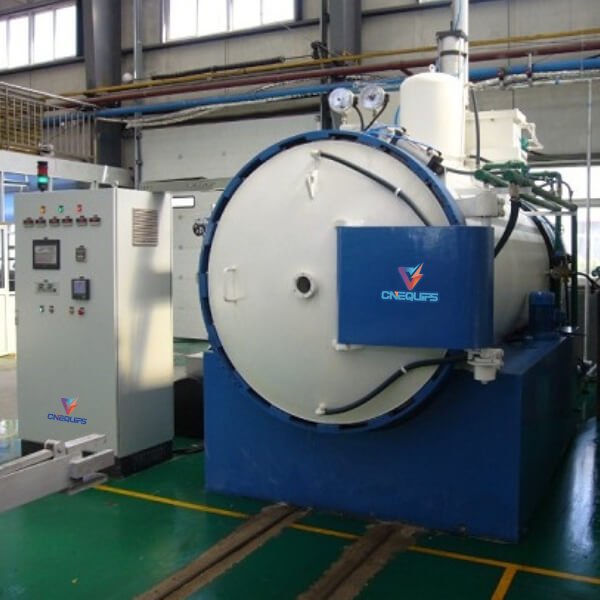